
SCARFING PLYWOOD
April 4, 2020
Why do we need to scarf plywood?
The beauty of boat building, I think, is you can break it down into a series of relatively simple, individual steps which eventually lead you to a complex shape that is both beautiful and functional (if you started with a good boat design, that is!). As I have learned over the course of building four smaller boats prior to Spencer and I starting in on Burnett, there are hard ways and easy ways to accomplish each individual step, and some steps are more crucial than others; some mistakes make later steps more difficult to complete, and some mistakes are not easily corrected, resulting in faults that are telegraphed through to the final product. Although the overarching goal of these posts is to provide a window into the project for interested family, friends, and strangers, we are also hopeful that the blog will serve as a resource for anyone looking to take on a stitch-and-glue boat building project themselves- somebody might as well benefit from the numerous mistakes we are sure to make! That means we will try to include enough technical details to satiate the appetite of a potential builder, but not so many that the resulting blogs are a snooze for someone just looking to follow along.
Before diving into how we glued plywood sheets end-to-end with scarf joints to make the ~40’ long panels that will eventually be Burnett’s hull, we need some context. What exactly is stitch-and-glue boat building? Below are photos of constructing Herbert, the first stitch-and-glue boat that my dad and I built back in 2011-2012. These photos capture the initial steps involved in building a stitch-and-glue hull. In the upper left photo, bulkheads are being set up on a building frame. The bulkheads are athwartship (side to side) structural members that stiffen the hull. Plywood hull panels cut precisely to fit the shape defined by the bulkheads are then bent around the bulkheads (center photo) and “stitched” together with wire at the seams between panels (upper right photo). Thus, one of the first steps in a build is to make plywood sheets that are long and wide enough to cut the bulkheads and hull panels out of. We therefore need to know how to scarf- the topic of this blog!
.jpg)
.jpg)
.jpg)

What the heck is a scarf joint?
Connecting two pieces of wood with a scarf joint involves cutting angled surfaces on the two pieces to be joined, applying glue to those surfaces, and mating them together (see below). Compared to a butt joint, the simplest of joints, a scarf has a larger surface area that is glued together and is therefore stronger. Additionally, a butt joint has a sharp discontinuity in mechanical properties, and strain is focused at this discontinuity when a bending force is applied. In contrast, scarf joints distribute strain resulting from a bending force over a larger area, resulting in smoother curves. Because we want the hull panels to be bent around the bulkheads into fair, gradual curves, the strength and uniform mechanical properties of the scarf joint are desirable.

Cutting Scarf Joints
Now that you know what a scarf joint is and why we need to join plywood sheets in this way, it’s finally time to cut into the wood that will become Burnett! This was a momentous occasion for Spencer and I, as the time and effort it took to get to this point far exceeded what either of us had imagined! Here is Spencer making the first cut:

One of the first lessons Spencer and I learned when we started building is never to assume that anything is square (not even a square sitting on the shelf at a hardware store!). Even though the plywood we are working with is the highest-grade marine pywood, it can be up to 3/16” out of square over 4’. How square the plywood is to start with impacts the quality of the resulting scarf joint, so the first step in the scarfing process was to square things off. We then arranged the plywood in a staircase-like fashion with a rise and run equal to the slope we wanted for the scarf joints (1:8). The next step was to use a power planer to quickly work the material down at approximately the desired slope. The plywood is a laminate of many veneers (9 in the case of the ½” plywood our hull panels are cut out of), and the grain of each veneer is oriented perpendicular to the veneers directly above and below it. This alternating grain orientation is one of the factors that gives plywood dimensional stability. When plywood is cut at an oblique angle to its veneers, as is the case in scarfing, the veneers become readily visible and can be used as a visual guide to maintain straight cuts; waviness in the lines bounding the veneers or variability in the apparent width of a single veneer indicate the scarf is being cut unevenly.
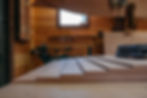



Once most of the excess material was removed with the power planer, we switched to a hand plane for more control when approaching the finished cut. The final step was to smooth things out with a belt sander.
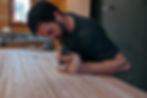




Gluing Scarf Joints
We glued our scarf joints together with marine epoxy. Marine epoxy is very strong and completely waterproof. It will be used extensively in the construction of Burnett (the designer estimates 150 gallons, which is about $15,000 worth!). Epoxy can be thickened with various additives to alter its consistency. The first step in gluing our scarf joints was to paint unthickened epoxy onto both surfaces to be joined and allow it to soak as deeply into the pore structure of the wood as possible. A layer of thickened epoxy was then spread on one of the surfaces being joined using a notched-tooth spreader, which is a great tool for quickly distributing a consistent quantity of thickened epoxy over the length of the joint. The two surfaces are then mated together and clamped. The thickened epoxy fills any irregularities in the joint and forms a strong chemical bond with the unthickened epoxy. Once cured (hardened), the unthickened epoxy locks into the pores of the wood, forming a strong bond between the epoxy and the plywood. The result is a sturdy joint that can withstand being bent around bulkheads into the fair curves we desire for our hull.


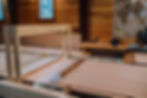


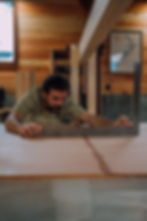


The Finished Product

Below are two slow-motion videos of me breaking pieces of plywood. In the video on the right is a piece of plywood with a scarf joint in the middle, and on the left a piece of plywood without any joints. Both pieces buckle and break in a similar fashion at the midpoint between my hands. As seen in the photo below the videos, the scarfed plywood broke across the scarf joint, not along it, indicating the scarf joint is stronger than the material it connects. All we can ask for!



Burnett has a total of eight hull panels (four on the port side, four starboard) and two panels that will be the sides of the keel, requiring a total of 34 scarf joints. A lot compared to the five scarfs needed for Herbert! The panels are also a lot longer- so long that a fair bit of logistics is involved when moving them around in our 20' by 56' shop. Here we are moving one of the smallest panels, the keel side, to the carport where it will be in Dad's way but out of our way (thanks Dad!) until we are ready for it:

We are now halfway through cutting hull panels from the scarfed-up plywood sheets. Stay tuned for a post detailing that process as well as a post about the spline joints used to connect ¾” plywood for the bulkheads!